Metalworking Fluids for CNC Machine
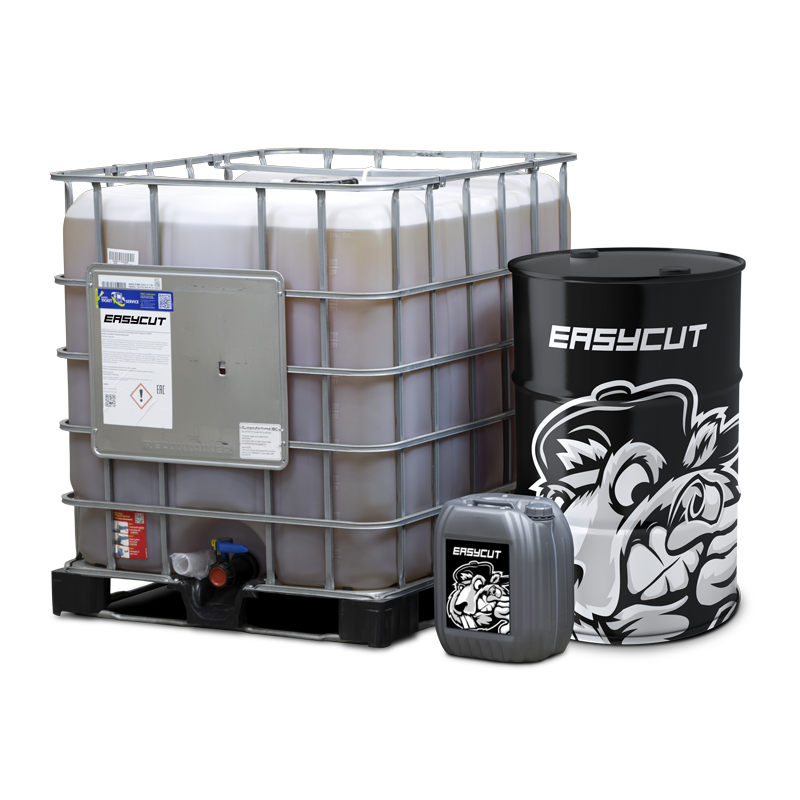
Welcome to EASYCUT coolant page, your one-stop destination for top-notch CNC fluids designed to optimize your machining operations. Explore our diverse range of fluids meticulously engineered to enhance performance and efficiency across various materials. Please check our fluids related articles for details:
Purpose of coolant Types of coolant Mixing and Water CNC machine cleaning TOP-UP Calculator
- 173,49 CA$ Price w/o VAT177,03 CA$
- 156,18 CA$ Price w/o VAT208,24 CA$UNI301-5In StockUNI301-5In StockTotal discount 25%Total discount 25%Total discount 25%
- 153,54 CA$ Price w/o VAT236,22 CA$PRO301-5In StockPRO301-5In StockTotal discount 35%Total discount 35%Total discount 35%
- 258,94 CA$ Price w/o VAT264,22 CA$SYN291CO-5In StockSYN291CO-5In Stock
- 168,61 CA$ Price w/o VAT172,05 CA$NMO121-5In StockNMO121-5In Stock
- 201,43 CA$ Price w/o VAT205,54 CA$NMO361-5In StockNMO361-5In Stock
- 323,31 CA$ Price w/o VAT329,91 CA$VEG001-5In StockVEG001-5In Stock
- 1 388,96 CA$ Price w/o VAT1 417,31 CA$NHO051-55Running out of stockNHO051-55Running out of stock
- 756,73 CA$ Price w/o VAT1 081,05 CA$EDM601-55Running out of stockEDM601-55Running out of stockTotal discount 30%Total discount 30%Total discount 30%
- 1 559,23 CA$ Price w/o VAT1 591,05 CA$NMO241-55Running out of stockNMO241-55Running out of stock
- 209,94 CA$ Price w/o VAT214,22 CA$ETAS0700-5Made to orderETAS0700-5Made to order
- 389,78 CA$ Price w/o VAT397,73 CA$FORM121-5Made to orderFORM121-5Made to order
The utilization of Computer Numerical Control (CNC) machines is a pivotal aspect of the metalworking process. However, the optimized performance of CNC machines relies on an often overlooked yet indispensable component: coolant fluids. CNC coolant plays a critical role in metalworking, significantly improving cutting performance and prolonging the lifespan not only of the machinery but also of the metal products themselves. In this article, we will delve into the significance and efficacy of coolants in metalworking, discussing the various coolant types and examining their respective functions.
The Multifaceted Role of Coolant
Coolant, alternatively referred to as cutting fluid or metalworking fluid, fulfills several crucial functions within the metalworking process.
-
Cooling: A primary function of coolant is to dissipate the heat that arises during metal cutting. The interaction between the cutting tool and workpiece generates friction and intense heat. Cooling properties mitigate thermal expansion, minimize the risk of deformation, and uphold dimensional accuracy.
-
Lubrication: Coolant fluids acts as a lubricant between the cutting tool and workpiece, reducing friction and minimizing wear. Its lubricating properties facilitate smooth and uniform cutting, prevent tool breakage, and enhance surface finish. By mitigating friction, coolant also contributes to improved energy efficiency by reducing the power required for machining operations.
-
Metal Removal: Metalworking fluids aid in the removal of metal chips and sawdust that accumulate during the cutting process. They flush these particles away from the cutting zone, preventing the formation of chips that could lead to tool wear, subpar surface finish, and potential damage to the workpiece.
Through the fulfillment of these functions, coolant fluids significantly enhances the overall efficiency and effectiveness of metalworking operations. Optimal coolant selection, as well as the proper maintenance of its concentration and cleanliness, are crucial for maximizing the benefits of coolant in CNC machining and metalworking processes.
Semi-synthetic fluids
Semi-synthetic coolants are a type of coolant commonly used in metalworking applications. They are formulated by blending mineral oil with synthetic additives, creating a hybrid fluid that combines the advantages of both oil-based and water-based coolants.
The advantages of semi-synthetic fluids are as follows:
-
Semi-synthetic coolants are characterized by their versatility, which allows them to be used for a wide range of machining tasks and materials.
-
The combination of mineral oil and synthetic additives in semi-synthetic fluids helps to reduce tool rattle, minimize edge build-up and improve chip evacuation.
-
They also provide excellent corrosion protection. Thanks to the content of rust and corrosion inhibitors, providing protection for both the machine and the workpiece.
The use of semi-synthetic fluids can be more expensive than traditional oil-based coolants. However, the many benefits they provide in terms of versatility, surface finish, tool life and corrosion protection make them a valuable investment for many machining operations.
Synthetic fluids
Synthetic coolants are a type of coolant widely used in metalworking. They consist entirely of synthetic base oils and additives, without the addition of mineral oil.
-
Synthetic metalworking fluids have excellent thermal conductivity, providing excellent cooling during machining, not only of the equipment but also of the workpiece itself.
-
As a rule, synthetic fluids require less maintenance than other types. They are less susceptible to bacterial growth. This reduces the need for frequent changes and simplifies maintenance procedures, saving workers time and effort.
-
Synthetic metalworking fluids have excellent chemical stability. They are less prone to degradation and do not degrade even under high temperature and pressure conditions.
-
Also, synthetic fluids have a low tendency to foam compared to other types of coolants.
Although synthetic fluids offer significant advantages in terms of cooling, lubrication and tool life extension, their higher cost and potential compatibility issues should be carefully evaluated.
Coolant fluid based on vegetarian (ester) oils
Coolants based on vegetarian or essential oils have a distinctive combination of properties that set them apart from other CNC coolants. This type is widely used in CNC machining and metalworking, provide a range of benefits:
-
Ether-based fluids prioritize environmentally friendly production methods, making them an ideal choice for companies seeking sustainability.
-
They also effectively protect both the CNC machine and the part being machined by effectively regulating and controlling temperature.
-
Given that this type of coolant fluid is formulated with esters, the fluid provides reliable protection against rust and corrosion, ensuring the longevity of the equipment and preserving the quality of the machined parts.
-
The ester oils retain their properties over time, providing excellent stability. This reduces the frequency of coolant changes and maintenance requirements, saving time and resources.
-
The most attractive factor for manufacturers is that ester-based fluids are compatible with a wide range of materials. This versatility makes them suitable for a variety of machining operations that utilize different materials and alloys.
However, it is important to note that the main disadvantage of ester-based fluids is their higher cost compared to other types of coolants. Despite this, they represent the most environmentally friendly option for CNC machining.
High Tech Synthetic fluids based on polymer
Modern synthetic fluids represent a significant advancement in technology. These mineral oil-free coolants are carefully formulated to meet the most stringent requirements of modern CNC machining and metalworking. Their distinctive formulation provides a number of notable benefits:
-
These coolants excel at handling the elevated temperatures encountered during CNC operations.
-
Thanks to new developments, they are easy to clean, which simplifies maintenance and promotes a cleaner working environment.
-
The unique formulation inhibits bacterial growth, creating a healthier and safer working environment for operators.
-
Fluids based on polymer offer reliable corrosion resistance, ensuring the longevity of the CNC machine and the quality of the parts being machined.
-
They also demonstrate remarkable compatibility with composite materials and plastics, making them well suited for machining operations involving these materials and providing versatility in their application.
However, it is important to note that their advanced formulations are more expensive than other fluids. Nevertheless, for operations requiring the unique properties of these highly advanced coolants, they represent a worthy investment in quality and performance.
Neat Oils / Oil Based Machine Fluids
Oil-based machine tool coolants, including pure mineral oils or ester oils, play an important role in CNC machining operations that prioritize lubrication. These fluids have a number of undeniable advantages:
-
The coolants have exceptional lubricating properties, effectively reducing tool wear and extending the life of machine parts.
-
Excellent for specific applications, such as dielectric fluids in electrical discharge machining (EDM) processes, they provide the necessary characteristics to work effectively in specialized environments.
-
Demonstrates remarkable stability, retaining the required properties even with prolonged use.
-
Ether-based oils, in particular, show a higher level of environmental friendliness, making them the preferred choice for environmentally friendly machining operations aimed at reducing environmental impact.
However, their limited water solubility and higher cost may pose challenges in some processing scenarios, requiring careful consideration of their suitability for specific applications.
In conclusion, the choice of coolant plays a decisive role in the efficiency and quality of CNC machining processes. In this article we have reviewed the main types of fluids, as well as their advantages and features.
Ultimately, the right choice of coolant helps increase productivity, reduce tool wear, extend equipment life and improve the quality of machined parts. Companies should carefully analyze their needs, business goals and environmental considerations to make an informed decision when selecting coolants, ensuring optimal results in their CNC machining processes.